StepLock Piston Seal Patent Information
Back to Steplock Piston Seal main page
To view this page as a print-friendly PDF click here
Prepared by Ed Danzer, January 28, 2003, US Patent No. 5,934,685
With current seal designs if the material used to seal pressure has enough tensile and yield strength to keep it from extruding or cold flowing through the running fit gap (fig. 1) at operating pressure above 4,000 psi, it cannot be a 1 piece seal or seal ring and still be installed in a 1 piece piston or gland groove.
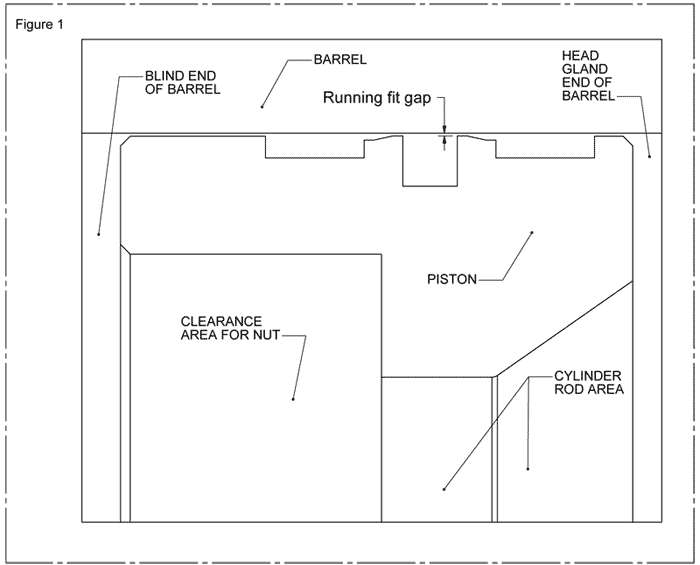
Our design allows for installation and the ability for the ring to expand when the barrel or gland expands from pressure. An example is, if a carbon steel tube has a 5 inch O.D. and measures 4.000 inches I.D. at 0 psi. internal pressure. When the pressure in the barrel increases, so does the bore size. Graph 1 shows the increase in bore size from internal pressure.
Graph 1
Increase in Cylinder Barrel Diameter from Internal Pressure
Poisson's ratio for carbon steel - v.300
Inside diameter of cylinder barrel - D 4.000 in
Thickness of cylinder wall - t0.500 in
Internal radial pressure - p0,1000..15000psi
Modulus of elasticity for carbon steel - E30000000psi
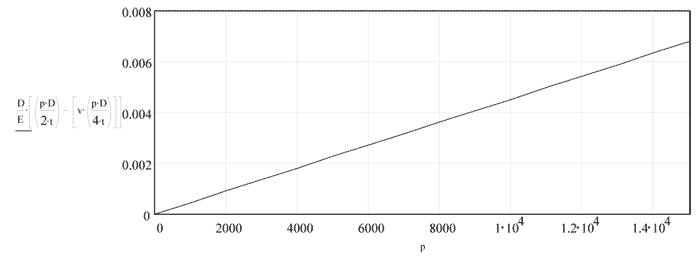
As the barrel expands from internal pressure the seal must expand radial also. With current designs a gap opens in between the steps. Graph 2 shows the increase in gap distance in relation to pressure. When pressure swells the barrel this gap opens up, the pressure forces the expander into this gap and when pressure is releases the gap closes and a bite of expander is taken out leading to expander failure. Machining male and female radii on the I.D. of the ring (fig.2) allow for ease of installation in a groove and also will seal off the expander flow as the feather edge of the female radius bends to contact the male radius. Even as the end gap increases from barrel expansion the female radius will continue cover the gap. Figure 3 shows the gap in the step of the ring assembly when pressurized to 15,000 PSI.
Graph 2
End Gap Clearance Increase Due to Cylinder Barrel Expansion from Internal Pressure
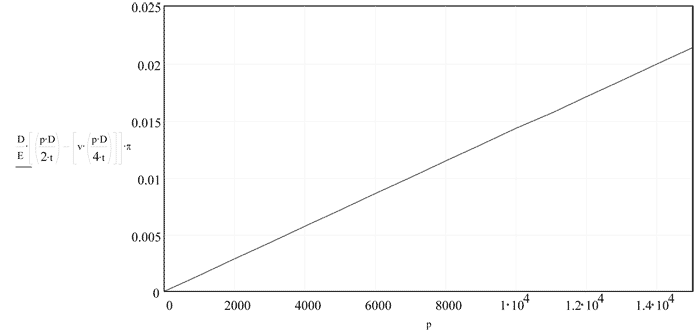
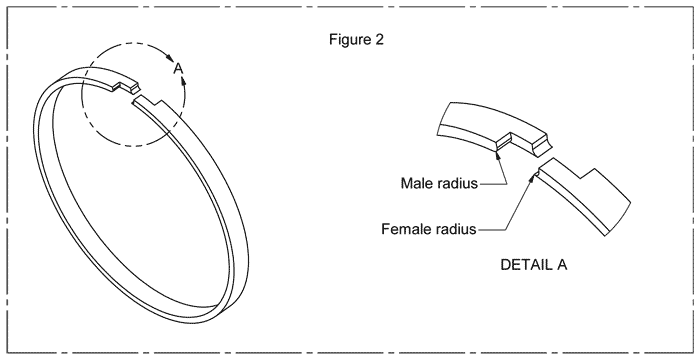
