DEHydS - Linear Engine
The original work was started in 1975 with the Danzer Cycle to be adapted to a small 1 cylinder engine. Because of limited resources and technology the project stalled until 2001. LEDHO, a Linear Engine with Direct Hydraulic Output was conceived as the best platform to increase the thermal efficiency of the internal combustion engine. A proof of concept engine was constructed and tested as a 4 stroke gasoline fueled engine in 2002.
The Danzer Cycle Linear Engine
This engine will work best in applications that need high energy density fuels and operate with varying power output requirements, such as:
- Automotive
- Power generation
- Construction
- Robotics
The Danzer Cycle Linear Engine Operation
This engine design uses two different thermal cycles to extract the most energy out of combustible fuels. First the engine is operated as a common 4 cycle internal combustion engine. Then, during the power stroke, water is injected into the combustion chamber shortly after ignition, converting it to a steam engine utilizing the waste heat that would go out the exhaust and cooling system in current engines.
A new way to extract only the power needed without much parasitic loss.
With computer control the fluid in the pumping assembly, the combustion process, and power output can be controlled more effectively. Any number of pumping units can operate independently, and combined for maximum energy efficiency under varying loads. Each pumping unit can have its own self-contained cycle control, and a master control can synchronize multiple units for greater output.
Only 3 primary moving parts reduces complexity and cost to manufacture.
There are only 3 primary moving parts in each pumping assembly: the piston assembly, an intake valve assembly, and an exhaust valve assembly. The only other moving parts are for control purposes and include fluid power control, fuel control, and water control. This simple design allows for total digital control of all engine functions including intake and exhaust valve timing, spark timing, piston speed, compression ratio, and the ability to adapt to different fuels without external changes.
Automotive application advantages are:
- A vehicle having multiple pumping units will only use the number required to do the work required. When stopped only 1 or 2 pumping units will fire to support electrical loads, during acceleration many will operate.
- With hydraulic accumulators to store energy, regenerative braking will increase overall efficiency of the vehicle.
- All wheel drive could be utilized to start the vehicle moving, at low speeds and slippery road conditions.
- Having individual pumping units will allow greater flexibility in design. The ability to place the pumping units separately in space, increase or decrease the number as units requires, and mix sizes of units will increase efficiency, and the value of the vehicle to the user.
Power generation application advantages are:
- With the power loss created by shipping power long distances during peak load, having each individual with the ability to produce only the amount of additional power required for their peak use on site would be beneficial.
- The excess heat could be used for hot water or space heating.
- Remote or job site power generation could see a large increase in efficiency during varying load. This system uses only the number of pumping units required, whereas current systems must keep all elements in motion even though they are not producing energy.
Construction equipment advantages are:
Even though most new construction equipment takes advantage of horsepower compensation in their hydraulic systems, our multiple pumping units can dramatically increase fuel efficiency, through reduction of parasitic loss, by using only the number of pumping units required to provide the flow and pressure needed for the task. With current systems the linear motion of the piston is converted to rotary motion by the crankshaft and then this rotary motion is converted to linear motion with a swash plate piston pump. All the components must be designed for operation under full power, yet will operate under reduced load. When a swash plate pump is de-stroked to reduce flow under partial load its operating efficiency is reduced dramatically. As the engine speed is changed, fuel efficiency will change. This can be expressed as lbs. Fuel/hp-hr, g/kw-hr or kg/kw-hr.
Robotic equipment advantages are:
Mobile robots need high energy density storage to operate for long durations, and reduced size. Most current robots use battery power storage, and electric motors for generating motion. These pumping units, if built small would allow fluid power to do the work, similar to construction equipment, thus reducing size, increasing operation efficiency and operation duration. With further refinement of the miniaturization of pumping units, the fluid power could provide power for insect robots.
Prototype construction and testing:
A proof of concept prototype has been constructed. Simple testing of the design has been done. The engine has been run with manual control of all functions and has run under computer control for several short time periods as a 4 stroke gas engine only.
States of Operation:
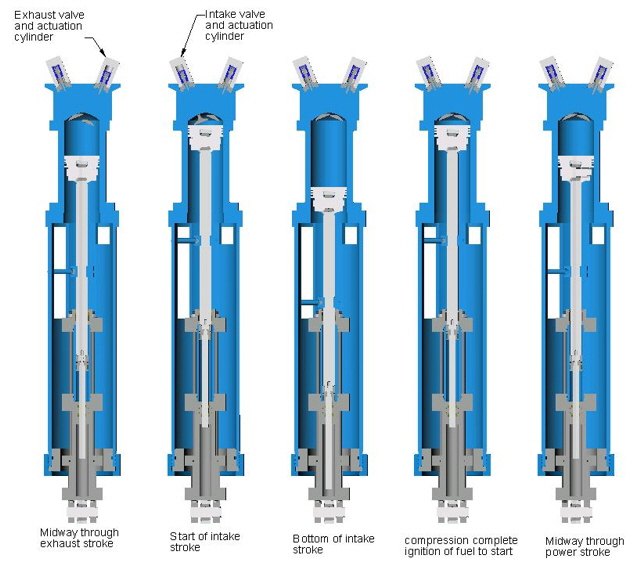
Proof of concept unit during testing
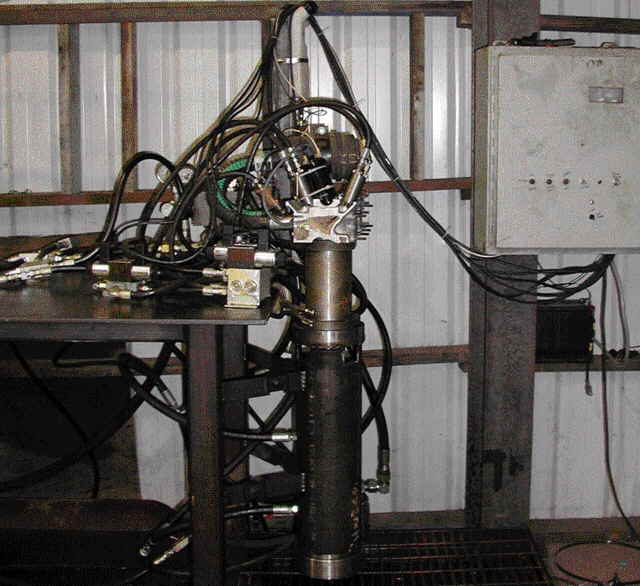
Close up of the proof of concept unit
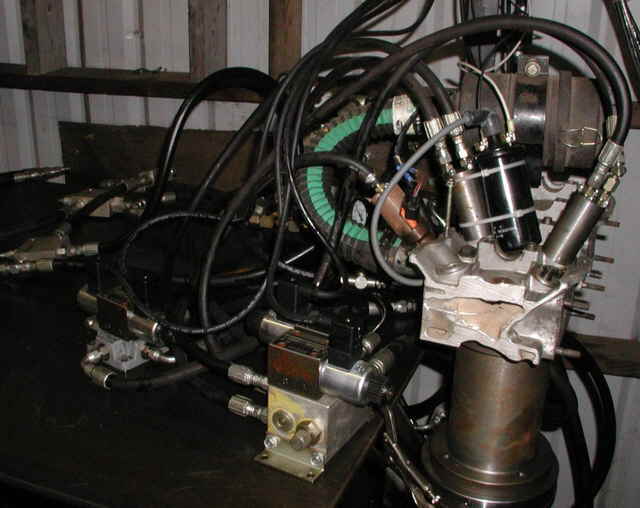